Sustainability Blog
The decision to build with mass timber and has many layers. It is not simply a matter of apparent first cost but also decisions about aesthetics, the environment, and sustainability.
And finally, the industry that designs and builds is itself changing. Design protocols and building codes are evolving.
Let’s take them in order:
- First cost
- Aesthetics
- The environment and sustainability
- Design and building codes
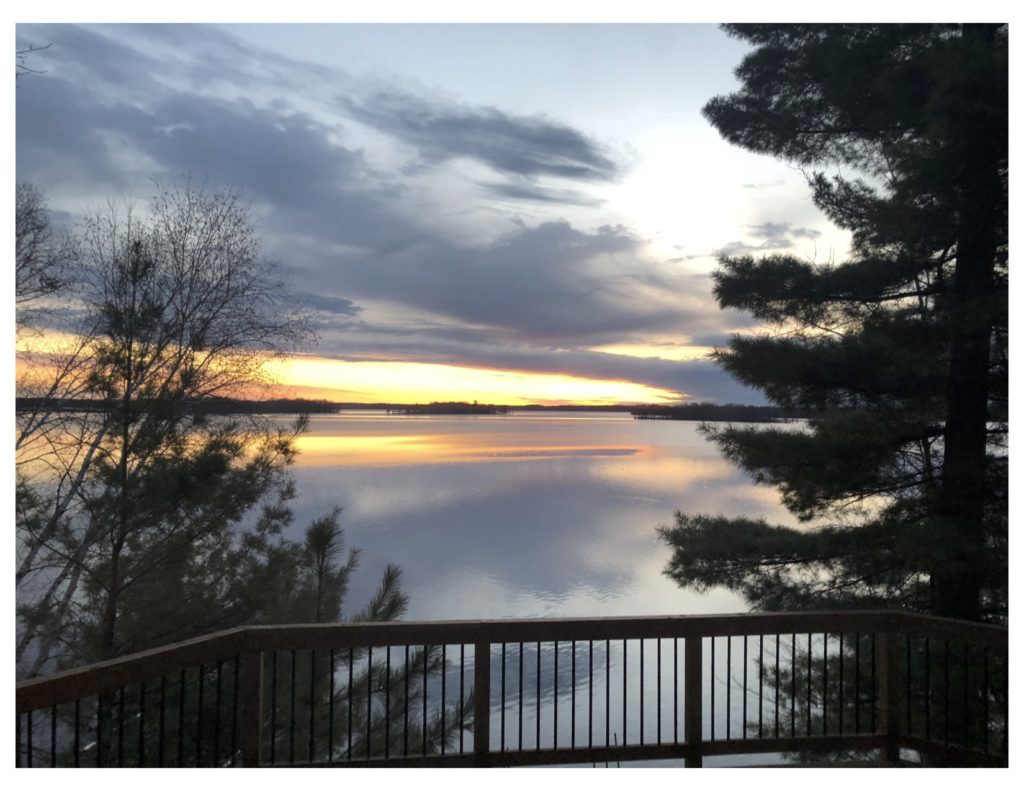
This post is written amid the COVID-19 global pandemic. This tragedy heightens awareness of how small and fragile this globe is and how much sustainability is essential in all matters.
I am a design-builder and see this matter through many layers but in the case of this post, I point out how intertwined solar energy and mass timber are as we all try to invent a future. Perhaps this future rides on the lessons of this spring and summer. Further, improved indoor climate is now critical. Here is a company that is responding: Schadegg Mechanical in St Paul, MN. They are evaluating various ways to improve indoor air quality including bi-polar ionization techniques:
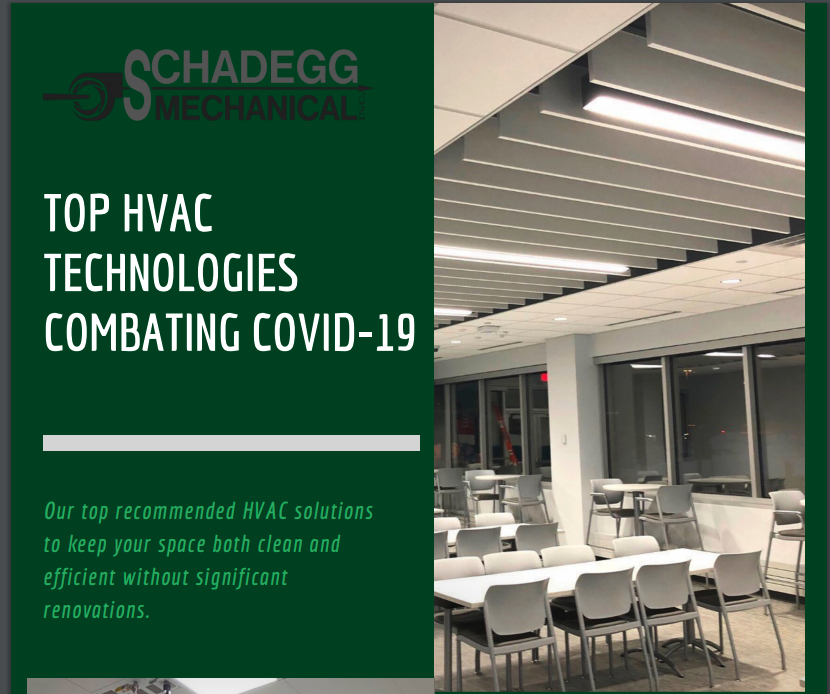
Additionally, the emerging mass timber and CLT design and construction technologies are now coming into their own. They are not the short term, low first cost choice but are the best for the planet in the mid and long term. See my post for a little more.
Lastly, the practical opportunities for what I call “organic solar” energy are passing the traditional financial engineering hurdles thanks to many federal tax law incentives and many programs operated by local serving utilities. In my lingo “organic solar” means photovoltaic solar energy generation systems that are integral to building and site, design and operations. They are best executed by “vertical stacks,: companies that plan, design, build, finance, and sometime own/operate. There are also emerging strategies that apply to retro-fit of existing buildings in addition to the typical roof-mounted solutions.
In other words: in the case of the future, it’s going to be different, like it or not. Sustainable building is inevitably in the mix.
Here are some of my posts on the matter. Note that I have included several in connection with financial management. They don’t attract the “reads” the way the timber and solar do but these actions are critical to turning the corner to feasible in ALL cases.:
Wood and heat pumps old made new again
The choice to build with mass timber
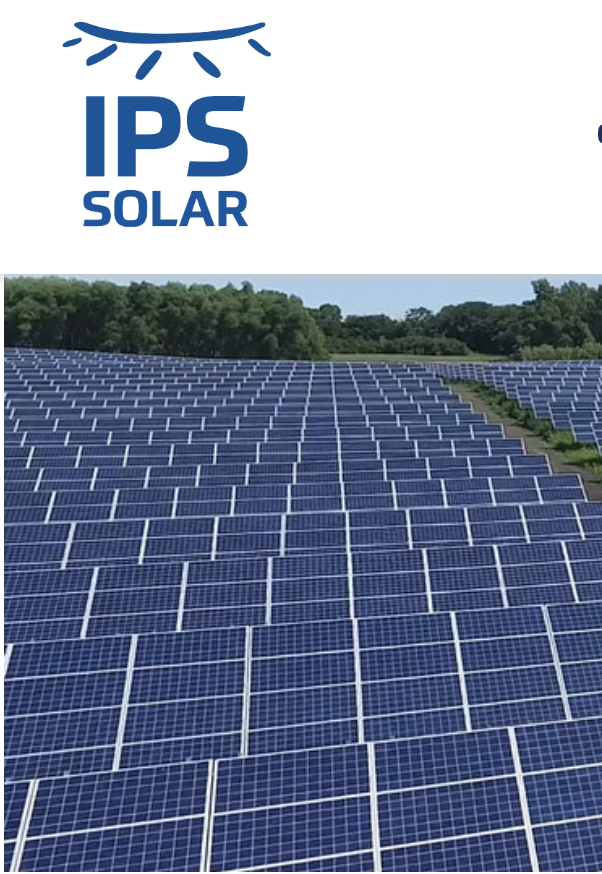
Application of solar energy collection and use into a building project involves a sequence of planning, design, construction, operational actions as well as financial engineering.
In the case of an existing site and building what constitutes “solar ready”?
- Is there physical space on the building or site in sufficient quantity?
- Open space on the site
- Roof space on the building
- Exterior wall space on the building
- If the building roof is to support solar arrays, is the roof configuration suitable to support the solar equipment?
- Is it strong enough?
- Is it not in shadow most of the day?
- Does the local serving utility offer financial incentives?
- Is the federal and state tax status of the building ownership such that tax incentives can be taken advantage of?
- Does it make sense for the owning entity to allocate its capital and credit-worthiness to the solar enterprise; i.e. is the pay-back period short enough?
In the case of a site and building project, all of the above considerations apply. However, there are additional advantages:
- The physical plan can be laid-out maximize solar collection potential without sacrificing other requirements
- The configuration of array’s supporting elements can be designed for efficiency, and cost effectiveness
- The solar configuration can be part of the aesthetic and architecture
With the above ideas in mind, it is also important to remember that the tax status of individuals and corporations are very different. This has a fundamental bearing on the “go, no-go” decision. Can various tax incentives be applied?
Lastly, working with an experienced entity that can deliver all aspects of a well-engineered financial and physical solution is a key to success. Plan thoughtfully and act purposely.
(Contact Steve Oman at IPS)
(Atlanta Botanical Gardens and Anderson Japanese Gardens Visitor Center)
A core mission at Wilkinson Building Advisors (formerly The Wilkinson Project Group) is to promote Wellness through the application advanced Mass Timber and Indoor Climate design and construction technologies. Though broadly applicable to wellness of persons and the planet, WBA focuses on education, health care, and housing. WBA works at the intersection of news, knowledge, collaboration, and best design and construction practices.
If you have read the post about “Successful Project Completion” then this post helps with some critical details: the concepts of FFE and fixed FFE (i.e. “Furniture, Fixtures, and Equipment”)
FFE (fixed or otherwise) is needed to complete your project and isn’t always expressly included in traditional design and construction services. Examples are:
- Security systems (designers and builders don’t want the liability)
- Data and communication systems (often part of the business work flow)
- Furniture and accessories (includes plants and specialties)
- Modular furniture and work stations (often called “cubicles”)
- Decorations (includes wall art)
- Special equipment (cooling systems for computer equipment etc)
At Wilkinson Building Advisors (“WBA”), projects have 3 stages:
- Planning and setup
- Execution and administration
- Project completion
This post is about Project Completion, the stage when the Owner has spent a lot of money and needs to move in and commence operations in order to derive value from the investment.
100 years ago, old-growth trees were used to make columns, girders, and planks for commercial buildings. Butler Square in Minneapolis is a good example of this applied construction technology. It was a sound construction strategy; 100 years of service is impressive. However, limitations arose from the availability of old-growth trees to be used for this purpose.
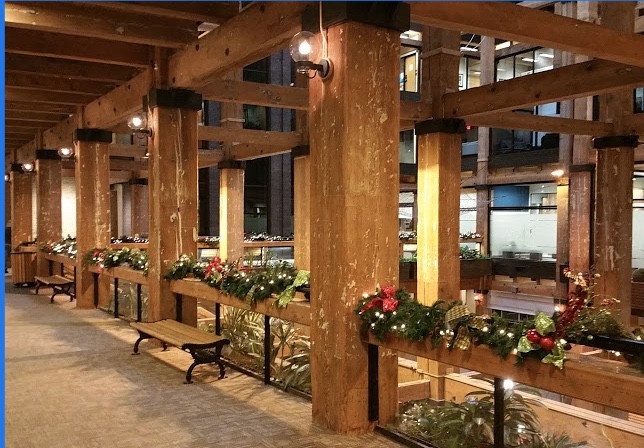
50 years ago mechanical designers in the Minneapolis area took the innovative step of applying emerging heat pump technology to indoor climate applications. It was revolutionary. Systems were simplified and installed costs plummeted. It was a serviceable technology for many commercial applications.
Fast forward to today, and the old is being made new again. The fabricated, structural timber industry now makes components to build frames and floors without relying on old-growth trees. To the contrary, 12 to 14-year-old trees are farmed and harvested to make glue-laminated products for the construction of timber frames and CLT floor systems (cross laminated timber).
Application of heat pumps is being used for high-efficiency indoor climate systems. The hydronic water piping systems move the energy around the building to where it's needed. The side of the building in sunlight sheds its excess heat (aka cooling) to the shaded side of the building requiring heating. This distribution by way of the heat pumps leads to reduced energy consumption for indoor climate and comfort.
It turns out that the many energy-saving advantages of wood when combined with high-efficiency indoor climate squarely addresses the issues of energy conservation needed in this era of global warming brought by man's activity.
Care taken in the building industry can make a big difference; join the movement!
(see the blog post at this site: “Timber and Advanced Energy Project Planned in the Upper-Midwest.”)
Cross laminated timber (CLT) is on a tipping point to bring big change to the midwest construction industry that builds in wood. On the face of it, CLT is just another wood floor product, but it is really more than that in many ways.
First the definition: CLT is a large flat panel made from smaller boards, arranged perpendicular to one another, and glued and pressed together. They come in various thicknesses from roughly 3” (3 ply) to 12” (7-9 ply), and in sizes up to 12’x 60’.
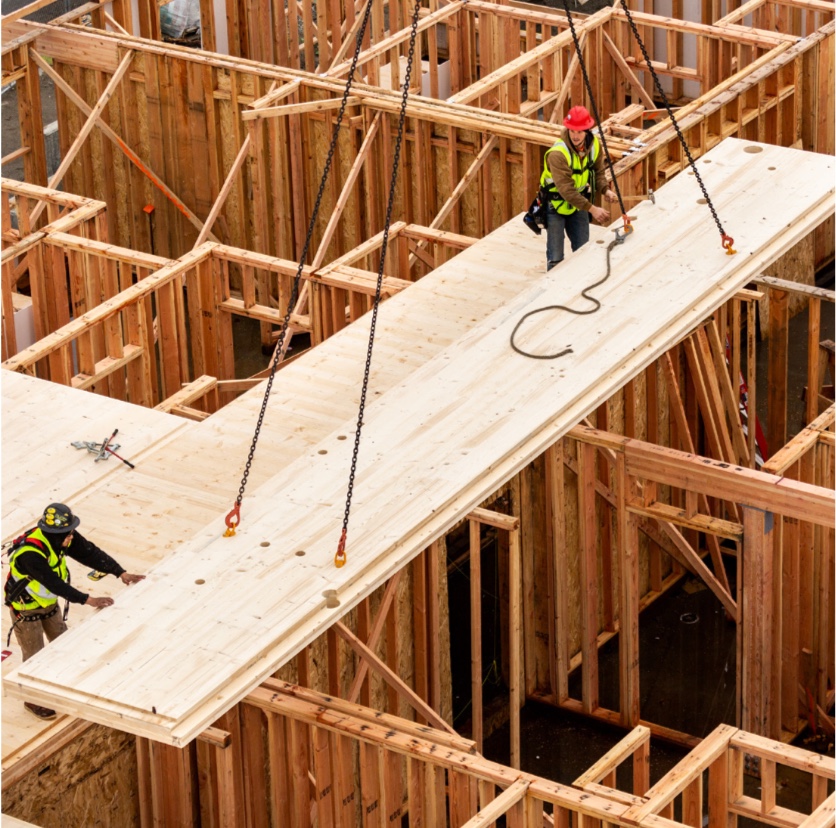
From structural engineering perspective, CLT offers a variety of layout patterns for strength and serviceability. From a construction engineering point of view, CLT can be revolutionary with respect to speed up construction. A small crew using light tools and assisted by mobile hoisting machinery can lift and place panels very quickly.
Developers also like CLT because it has the potential of saving building height while preserving volume within the building. After all volume is what brings the rent not building height. The tenants who pay the rent also tend to love the look and feel of the wood ceilings (the exposed underside of CLT floors).
CLT got it started in Europe and then migrated to the Pacific Northwest and West Canada. It's in these locations that plants have sprung up in many projects using CLT have been built. Now the time has come for the Midwest to join the CLT club as the production and distribution systems expand.
Wilkinson Building Advisors is working with various organizations including Katerra based in Seattle to bring the first demonstration projects to the Midwest. Katerra's local representative in the midwest is Pete Kobelt at pete.kobelt@katerra.com. Pete has deep experience with CLT products.
More...
Timber and advanced energy project planned in upper-midwest
George WilkinsonWilkinson Building Advisors (formerly Wpg Ltd) is in ongoing conversations and exchange of documents with the several government and private investors in connection with creating several demonstration projects in the upper Midwest.
- The concept is that these projects would engage several intersecting technologies to create low carbon footprint buildings. These technologies are:
- Glue laminated mass timber frames (Glulam) and cross-laminated (CLT) timber floor systems and shaft walls (to resolve lateral loads)
- Structural integrated panels (SIPs) for exterior wall and roof panels (structural integrated panels)
- Interior climate systems (energy exchange, distribution, and ventilation) including technologies to measure/control/report energy consumption in hydronic systems
- Computer-based design and manufacturing control systems
- The combination of the these systems is synergist with respect to reducing the carbon footprint of these buildings:
- Sequestering CO2 in the timber products
- Avoidance of energy expended in concrete production and steel assembly fabrications when appropriate
- Application of enclosure systems designed for extreme climates
- Design of indoor climate systems based on passive, sustainable solutions and using systems avoiding combustion based energy exchange
- "Tinker-Toy" precast concrete assemblies for podiums and selected lateral load resisting systems
- "Building in a box" construction management techniques; sequential shipment to tight sites, erection by small efficient crews
- A high degree of off-site completion for the "kit of parts" as well as modular assemblies
- The scale and geographic distribution of these projects is intended to showcase the possible and bring the market to a tipping point. These initiatives target 2 prototypical markets
- Urban, infill, mixed use; small scale, 40-75,000sf, 3-5 stories; suitable for building in congested and complex urban environments
- Private higher education, classroom addition or environmental science building; embodying the sense of mission of the institution
- Here are snippets of the ideas from Woodworks, a leading building advisory group:
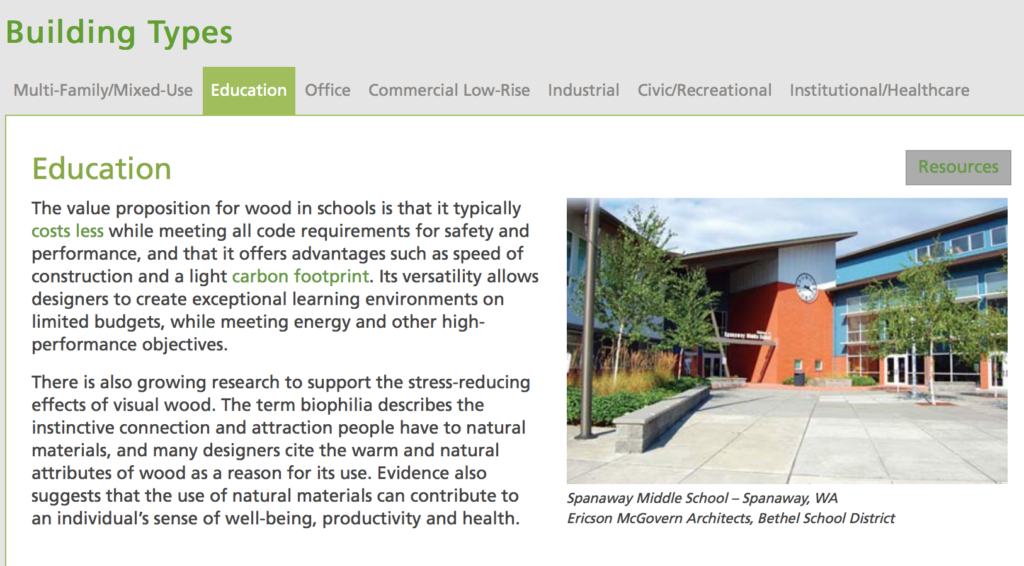

This author believes that demonstration projects, well executed, can attract the attention of both policy and market-makers. The walk-through, “touch and feel” experience of these proposed and delightful places can be compelling. As the marketing folks would say: it makes the intangible… tangible.
This is a chance to engage a far-flung industry to plan for the benefit of the planet and the quality of life in the upper-midwest. Join the movement!
For Investors; manage your risks, know your costs upfront
George WilkinsonA contract is an agreement about how risk is allocated in the deal; risk is priced into the deal. Each party to the contract negotiates for, and eventually agrees to the price of performance. The specter of risk sits on the shoulders of the contracting parties. When risk is substantially speculative, as compared to known, then contract negotiations and subsequence performance are distorted.
Many processes in the AEC+dev industry are “poster children” to the proposition of contract and performance distortion resulting from mis-allocated risk. Cost ignorance is high among the usual suspects.What is the probability of project successful when this outcome is premised upon blind hope in lieu of skilled calculation?
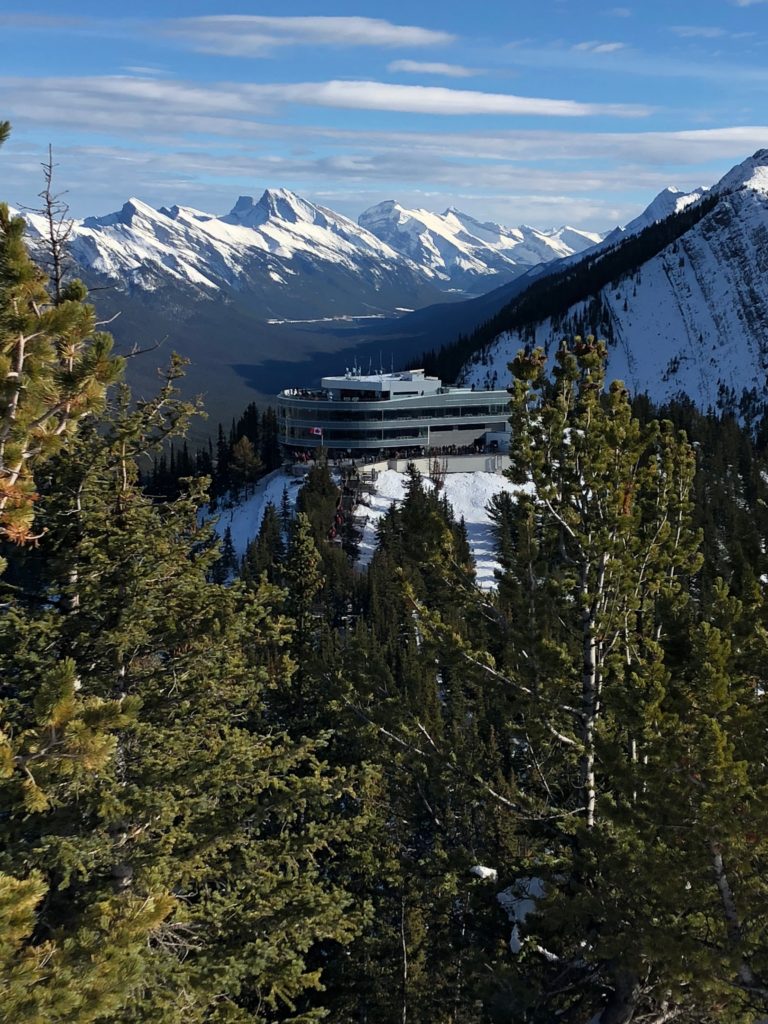
Gunter Dittmar was my icon in graduate school. He was a despondent German expatriate bombed into depression while growing up in Berlin during the Allied blitz. Amid his slow and thoughtful speech was a bit of genius. He understood that the "problem solving process" and the “problem seeking process” involved keeping the "levels of abstraction" aligned and not mixed up.
For example, you can't solve the big picture if you're focused too early on how many doorknobs and how much they cost each. Ultimately you care about the doorknobs, but only in the right sequence and at the right time.
“The is nothing more worrisome that the wrong question answered well” (quote from South American Architect on TED talks)
The reasons for the mix-ups are many are 1) participants competing for influence in the process and sowing mixed levels just to be in the conversation, 2) sometimes the logical structure of the issue is simply misunderstood and the conversationalists get down the rabbit hole, 3) the participating silos have standards of practice that run in opposition to one another, 4) the participants don't like one another, and 5) disorderly allocation of risk (hours of effort in dollars) etc .
In any event put first things first as you move from concepts to details.
(For purposes of this document, planning, design, construction, and development of real property (a.k.a. buildings) will be referred to as the “AEC” industry.)
It is common that many customers to services in the AEC industry seldom do business there and in many cases the project undertaken is a "one-off." Furthermore, these customers find themselves in the position of attempting to manage many intertwining contracts while all at the same time successfully operating the business that brought them to needing more in the way of property (buildings). These conditions, in and of themselves put up barriers to success, but there are more equally significant obstacles lurking at the outset.
Essay to Investors: Save the planet with timber and energy design
George WilkinsonApplied technology in the building industry is now at a tipping point. The intersection of timber construction technologies with indoor climate energy exchange and management is creating powerful new market opportunities.
When design-build is good, it can provide a groundswell of innovation
George WilkinsonThe cultural headwinds have long been on the bow of the so-called design-build movement. It took nearly 50 years of cultural warfare for the various participants to see their integrative potential. It is easy to see how the cultural divide is built into the DNA of the various designers, engineers, builders, salespeople, financial engineers, and business managers; they are all different people with different worldviews and ways of behaving. The marketplace finally demanded cooperation and collaboration. By the 1990’s, the acceptance of the design-build approach was no longer in dispute.